Hypersonix Development of CMC and UHTCMC has expanded significantly as the U.S. Department of Defense (DOD) seeks to counter threats from hypersonic weapons. Hypersonic speeds are not only reached by current long-range ballistic missiles, but also by reentry and space launch vehicles, like the SpaceX Falcon. The rapidly expanding New Space market is thus also driving new hypersonic technology. Straddling both markets is Hypersonix Launch Systems (Brisbane, Australia) and its three hypersonic vehicles based on a patented hydrogen-fueled scramjet engine called Spartan that produces no CO2 emissions. Hypersonix states its mission is to provide reusable space launch technology that is sustainable. The company was founded in 2019 to commercialize 30 years of development by cofounder Michael Smart, whose research spans NASA Langley and the renowned Hypersonics Research Centre at the University of Queensland (Brisbane, Australia). In March 2023, Hypersonix was selected from 63 respondents to provide hypersonic vehicles for the DOD’s Hypersonic and High-Cadence Airborne Testing Capabilities (HyCAT) program, overseen by the DOD’s Silicon Valley-based Defense Innovation Unit (DIU).
The vehicle chosen by HyCAT is Dart. “It is designed to be an affordable, single-use test platform,” says Andy Mulholland, head of product for Hypersonix. “Its small size doesn’t allow for the equipment needed for recovery and reuse. But the next two vehicles are reusable: VISR, which stands for Velos intelligence surveillance reconnaissance, and the Delta-Velos Orbiter. Both will return to land on a runway. VISR is a hypersonic UAV [unmanned aerial vehicle] and Delta-Velos is our highly reusable and highcadence solution for delivering small satellites to orbit.” While Dart is fully 3D printed from Inconel metal alloy, VISR and Delta-Velos will need CMC to address the very high temperatures they will encounter at the faster speeds needed to access space and reenter Earth’s atmosphere, explains Sam Grieve, manufacturing lead at Hypersonix. “If we didn’t use CMC, we’d need an ablative TPS like other spacecraft.” Vaporized during reentry, ablative TPS must be re-applied, which adds complexity, weight and cost. High-temperature CMC (HTCMC) is a better solution, he says, “to handle temperatures that are generated from friction with the air, but also from combustion inside the engine.” To that end, Hypersonix recently received a C/SiC demonstrator part that was designed in-house but produced, notes Smart, “using a very complex, never-done-before process working very closely over the last 2 years with a team of experts in Germany.”
The C/SiC part is a Spartan scramjet combustion chamber (Fig. 2) that is expected to handle temperatures up to 1,400°C. “It’s a manufacturing demonstrator that teaches us about the material and the technology,” says Grieve. “We’re hoping to eventually have these parts produced here by a local supply chain, but we may also produce some parts ourselves.” Mulholland notes it’s not a flight piece, “but is just to demonstrate that we could make the variable and intricate geometries needed. C/SiC was chosen as a more basic and well-understood HTCMC to start with, but eventually we’ll need much higher temperature materials.” Where will these materials be used? “First for parts where combustion is occurring,” says Grieve, “and then other parts of the engine, followed by airframe leading edges that are directly exposed to hypersonic air flow.” Will Dart use a CMC combustion chamber in its Spartan engine? “Not in the engine,” says Grieve, “but we are planning for parts like leading edges. CMC technology is important for enabling reusability, but that’s not required for our first Dart vehicles. Our HTCMC demonstrator and development now is to prove out technology we’ll need as we move forward.” The Dart’s first flight via the HyCAT program is planned for 2024 using Rocket Lab’s (Long Beach, Calif., U.S.) Hypersonic Accelerator Suborbital Test Electron (HASTE) rocket as a booster. Grieve explains why. “Spartan produces thrust as air enters through an inlet, gets compressed, then injected with fuel and combusted, which adds energy to the air flow, and then expands as it exits the nozzle. But unlike a turbojet, we have no moving parts — our compression is done by shockwaves which come off the front of the vehicle. The booster gets Spartan to the speeds above Mach 5 that it needs to operate.” In August, Hypersonix announced an exclusive teaming agreement with Kratos Defense & Security Solutions (San Diego, Calif., U.S.). “This is complementary to our contract with DIU,” says Mulholland, “and gives us another channel for commercialization. Kratos also has a lot of experience in the space market and their Zeus rockets can also be used as a booster for Spartan.” These first contracts are a key step in the company’s vehicle development. “As we continue to develop VISR and Delta-Velos, we’ll be running up against the limits of materials technology pretty quickly,” says Grieve. “There’s a nonlinear increase in temperature with Mach number, and our scramjet engine is designed to operate up to Mach 10, and we think even Mach 12. So, we’re going to reach pretty crazy temperatures sooner than later, and we’ll need to find and prove out new HTCMC and UHTCMC materials.”
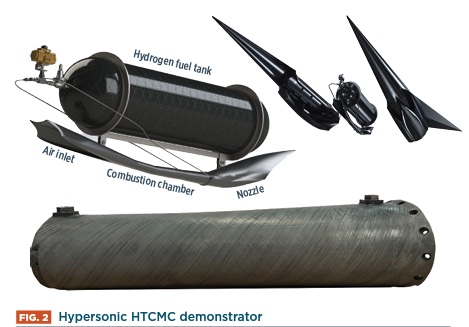
To find out more about the global composites market and keep up with news, head to the below: