HYPERSONIX LAUNCH SYSTEMS’ motto is Fly to Space, but that’s not its only vision. The Australian aerospace company focuses on developing cost-effective launch systems to place satellites in low earth orbit (LEO). However, joint-founder and head of research and development, Michael Smart believes the technology currently being developed will have long-term implications for air travel as it could be used on commercial aircraft. In future, flying from Sydney to New York in two to three hours could be possible with an airliner flying at hypersonic speeds.
At the core of Hypersonix’s activities is the SPARTAN scramjet (supersonic combustion ramjet), which requires a minimum speed of Mach 5 to operate and can thrust a vehicle to Mach 12.
Smart’s 30 years of experience in scramjet technology through extensive test and evaluation has provided specialist knowledge of the dynamics involved in producing a successful scramjet. The limitations of materials used in engines and on external flight surfaces to operate at the elevated temperatures of hypersonic (above Mach 5) speeds have led to the development of special alloys and composites. In addition, manufacturing technology has introduced new processes, improving the product’s quality and efficiency.
The use of 3D printing or additive engineering, as it’s known, to manufacture the fixed internal geometry of a scramjet has reduced costs and has the added advantage that design changes to the engine geometry can be achieved quickly.
Before scramjets, ramjets were used predominately to propel surface-to-air missiles to supersonic speeds and first came to prominence in the 1950s and 1960s. An early example was the Bristol Bloodhound which used four solid-fuel expendable rockets and two Bristol Thor ramjets. Air-breathing ramjets have no moving parts and work by compressing supersonic air to a subsonic high-pressure state to achieve combustion and thrust.
A scramjet has many features of a ramjet but can operate hypersonically. The engine accepts supersonic airflow and produces shock waves, via a shock train in the engine inlet, that promotes efficient combustion and delivers progressively increasing thrust. Scramjet operation is optimised at a high Mach number and makes the engine an ideal match for Hypersonix’s Fly to Space objectives.
Early Scramjets
The development of scramjets goes back to 1987 with the T4 free piston shock tunnel at the University of Queensland pioneered by Professor Ray Stalker. The Stalker tube, as it was known, performed more than 10,000 ground shot tests and provided a springboard for more in-depth exploratory projects.
Follow-on programs, such as the University of Queensland’s 2002 HiShot program and a more extensive project, HIFiRE 2007, were carried out with the assistance of a rocket that carried the scramjet to the required speed and altitude test conditions.
The NASA X-43A project was the first scramjet-powered vehicle to fly independently, reaching Mach 6.8 for 11 seconds in 2004. A later test achieved a speed of Mach 9.8, which remains the record for an independent scramjet-powered vehicle.
Sustainability
Launching satellites into LEO is currently an expensive business requiring large volumes of fuel and high thrust, typically delivered by multiple rocket stages that are discarded after stage burn-out. The actual satellite payload typically amounts to just two percent of the total launch mass. Rocket propulsion has been the standard launch technique since the 1960s and apart from cost and in efficiency has some significant adverse environmental effects.
Hypersonix is committed to flying to space using scramjet power rather than conventional multistage rocket thrust to satisfy the launch to LEO objective.
Scramjet engines are fuelled by hydrogen which emits only water vapour when burned. Initially high-pressure hydrogen gas will be used, but further developments will introduce liquid hydrogen. Ultimately, hydrogen produced using renewable energy for electrolysis to generate H2 from seawater will be used. The company puts an emphasis on environmentally sustainable techniques in all facets of its business and launch-platform reuse is central to its development objective.
Over many years, a significant mass of debris has been left in space, mostly in low orbit and Hypersonix is determined its vehicles will not add to the problem. “We return 98 percent of what we send into the atmosphere and beyond,” says Smart.
The SPARTAN
Hypersonix development activities have advanced several innovations not previously applied in space technology. The core development is the SPARTAN, a self-igniting, hydrogen-fuelled scramjet and the world’s first 3D-printed engine using high-temperature metal alloy. SPARTAN delivers a high strength-to weight ratio configuration and the ability to perform at the elevated temperatures of hypersonic flight. The engine has been mated to a three-metre-long flight vehicle, DART AE, also constructed from a high temperature alloy.
Against stiff competition, Hypersonix won a significant order from the US Defence Innovation Unit (DIU) for a hypersonic vehicle to explore the characteristics of the hypersonic environment. The DIU will take delivery of DART AE demonstrator vehicles in 2024 to satisfy the requirements of the US High-Cadence Airborne Testing Capabilities (HyCAT) program. The DART AE provides the ideal platform to present a non-ballistic, hypersonic flight profile at speeds up to Mach 7 and for up to 400 seconds. DIU will test sensors, communication systems, navigation and guidance components repeating flights at short intervals.
Hypersonix Head of Product, Andy Mulholland says: “I believe we have a common road map with DIU, and our innovation in hypersonic technology together with our flight test program aligns closely with their requirements”.
Launch Systems
Velos Intelligence Surveillance Reconnaissance (VISR) is a larger sustainable flight demonstrator at 5.5m long with a wingspan of 2m. It’s powered by four SPARTAN fifth-generation hydrogen-fuelled scramjets, enabling acceleration from Mach 5 to Mach 12. The vehicle has a delta planform, performs like a plane, and can be returned to a conventional runway. As a non-ballistic, manoeuvrable vehicle, VISR can turn into and deliver a 50kg payload to any required LEO station.
The Delta Velos Orbiter, a 12m long, 3.5m wingspan delta-shaped aircraft and a larger version of VISR is designed to launch small satellites of up to 150kg. The orbiter can be scaled up to accommodate satellites up to 300kg. The Delta Velos Orbiter benefits from a plug-and-play approach allowing access to any orbit from any launch site reducing launch costs and timescales.
Hypersonix has developed a three-stage launch system identified as Wirraway. Wirraway uses a small, conventional first-stage rocket incorporating a few Hypersonix modifications, dubbed Boomerang, to boost the Delta Velos Orbiter to the first-stage velocity of Mach5, at which point Boomerang is jettisoned, enabling it to glide back to Earth for reuse. The SPARTAN-scramjet powered orbiter then accelerates to the desired launch speed up to Mach12 before deploying a small kick stage rocket to insert the satellite into orbit. The Delta Velos Orbiter then returns to Earth on a pre-determined path.
Future Developments
Hypersonix is in collaboration with like-minded partners to further develop composite materials that will enable reliable scramjet operation at higher speeds and temperatures, and has opened an office in Munich, Germany. “We were already in discussion with several German companies involved in composite materials, and it made sense for us to be at the heart of this technology with our own office,” Smart says.
A key company objective is to pursue a small slice of the expanding multi-billion dollar launch to LEO market. The first demonstrator order from DIU indicates the potential within the worldwide defence industry and will help establish a solid base for future growth.
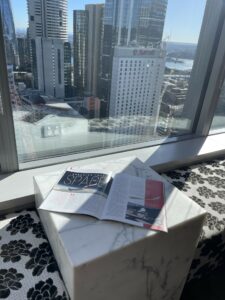
About Hypersonix
Hypersonix manufactures and operates hydrogen fuelled scramjet powered Unmanned Aerial Vehicles. These provide a modular solution to the commercial and military markets.
Media contact:
Nina Patz, Email: Nina.Patz@hypersonix.com